ابزار برش از چه موادی ساخته میشوند

کربن استیل
کربن استیل از سال 1880 در ابزار برشکاری مورد استفاده قرار گرفته است. اما کربن استیل در دمای 180 درجهی سانتیگراد شروع به نرم شدن میکند. این محدودیت بدین معنا است که این نوع ابزار به ندرت برای برش فلزات مورد استفاده قرار میگیرد. ابزار کربن استیل ساده حاوی 0.9% کربن و حدود 1% منگنز است که به درجه سختی 62 Rc رسیده و بیشتر برای کار با چوب مورد استفاده قرار میگیرد.
فولاد با سرعت بالا یا HSS
دلیل نامگذاری این ابزار با این اسم این است که برای برشکاری با سرعت بالا ساخته شدهاند.HSS در سال 1900 ساخته شد و پر آلیاژترین فولاد را دارد. در ابتدا تنگستن یا سریT ساخته شدند که عموما حاوی 12 تا 18% تنگستن به اضافهی 4% کرومیم و 1 تا 5% وانادیوم است. اکثر درجات آن حاوی حدود 0.5% مولیبدنوم و 4 تا 12% کبالت است.
طولی نکشید که معلوم شد اگر تنگستن با مولیبدنوم جایگزین شود، مقاومت در برابر ساییدگی در مقایسه با سری T بیشتر میشود و در برابر گرما به میزان کمتری شکل خود را از دست میدهد. در نتیجه حدود 95% ابزار HSS با درجات سری M ساخته میشوند. این ابزار حاوی 5 تا 10% مولیبدنیوم، 1.5 تا 10% تنگستن، 1 تا 4% وانادیوم، 4% کرومیوم و بسیاری از درجات دیگر حاوی 5 تا 10% کبالت هستند.
ابزار HSS سخت بوده و برای برشکاریهای منقطع مناسب هستند و برای ساختن ابزاری که شکل پیچیده دارند مثل دریل، برقو، شیر، سرپیچ و دنده تراش مورد استفاده قرار میگیرند. برای اینکه این ابزار در برابر ساییدگی مقاوتر شود ممکن است روی آنها پوشش قرار گیرد. HSS بیشترین استفاده را از لحاظ وزنی دارد. سرعت برش معمولا از 10 تا 60 متر در دقیقه است.
آلیاژهای کبالت
این آلیاژها در دههی 1900 به بازار آمدند و حاوی ترکیباتی چون 40 تا 55% کبالت، 30% کرومیوم و 10 تا 20 % تنگستن هستند و گرما هیچ تاثیری روی آنها ندارد. بیشینهی سختی این آلیاژها 55 تا 64 Rc است. آلیاژهای کبالت مقاومت بالایی در برابر سایش دارند اما به سختی HSS نیستند ولی میتوان آنها را در سرعتهای بالاتری از HSS مورد استفاده قرار داد. در حال حاضر استفاده از این آلیاژها بسیار محدود است.
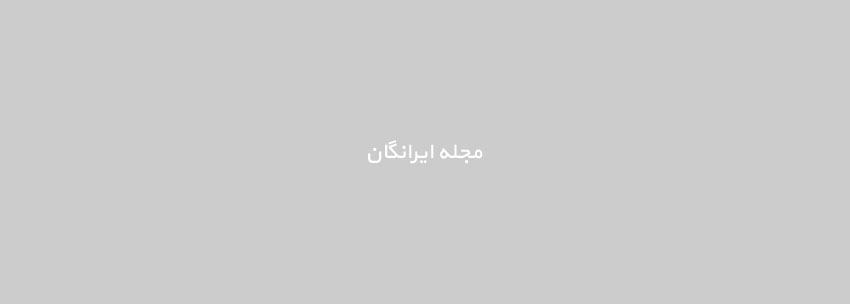
کاربیدها
کاربیدها در دههی 30 میلادی وارد بازار شدند و در برابر درجات مختلف گرمایی مقاومت زیادی دارند؛ رسانایی گرمایی آنها بالا است و مدول یانگ بالا، آنها را به موادی موثر برای ساخت ابزار بدل میکند و کاربردهای زیادی دارند. دو گروه از کاربیدها که برای ماشینکاری مورد استفاده قرار میگیرند عبارتند از کاربید تنگستن و کاربید تیتانیوم که هر دوی آنها میتوانند روکشدار یا بدون روکش باشند.
ذرات کاربید تنگستن در ماتریکس کبالت با استفاده از متالورژی پودر با هم پیوند برقرار میکنند. پودر فشرده شده و همجوش میشود. درجات مختلفی از آن برای کاربردهای مختلف موجود است. ابزاری که نوک کاربید همجوشی شده دارند، در برشکاری فلزات بیشترین استفاده را دارند. میزان کبالت موجود در ابزار کاربید تاثیر زیادی در جنس آن میگذارد. 3 تا 6% ماتریکس کبالت سختی را بیشتر میکند در حالی که 6 تا 15% ماتریکس کبالت مقاومت را بیشتر میکند اما سختی، مقاومت در برابر سایش و استحکام آن را کم میکند. ابزار کاربید تنگستن عموما برای ماشینکاری فولاد، چدن و مواد غیر آهنی ساینده به کار میرود.
لایه نشانی
روکشها اغلب در قسمت نوک ابزار کاربید مورد استفاده قرار میگیرند تا عمر آن افزایش یافته و همچنین عمل برشکاری با سرعت بیشتری انجام گیرد. ابزاری که نوکشان لایه نشانی شده نسبت به ابزار با نوک بدون لایه نشانی 10 برابر بیشتر عمر میکنند. مواد روکش عموما عبارتند از نیترید تیتانیوم، کاربید تیتانیوم و اکسید آلومینیوم که معمولا به ضخامت 2 تا 15 میکرو متر است. اغلب بسته به نوع کاربرد نوک ابزار، از چند لایهی مختلف استفاده میشود که یکی بر روی دیگری قرار میگیرد. تکنیکهای مورد استفاده برای لایه نشانی عبارتند از رسوب بخار شیمیایی یا CVD، CVD به کمک پلاسما و رسوب بخار فیزیکی یا PVD.
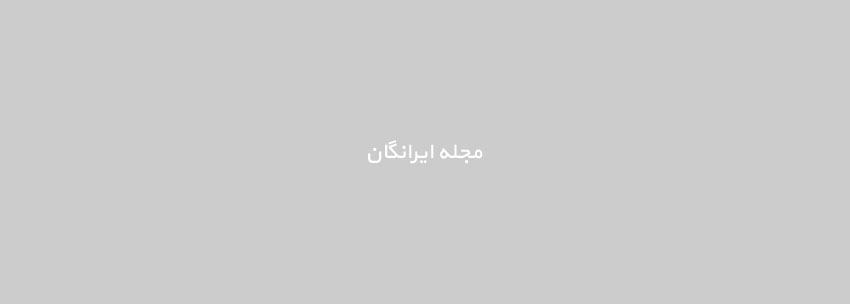
سرمتها
این مواد که در دههی 60 میلادی تولید شدند عموما حاوی 70% اکسید آلومینیوم و 30% کاربید تیتانیوم هستند. برخی از فرمولها شامل کاربید مولیبدنوم، کاربید نوبیوم و کاربید تانتالوم است. عملکرد آنها بین کاربید و سرامیک قرار میگیرد. سرعت برش آنها 150 تا 350 متر در دقیقه است.
سرامیک-آلومینا
این ماده در اوایل دههی 50 میلادی به بازار آمد و دو درجه از آنها برای برش مورد استفاده قرار میگیرد. یعنی اکسید آلومینیوم دانه ریز با خلوص بالا و نیترید سیلیکون فشرده شده که در دمای بالا همجوش میشود. برای بهتر شدن آن ممکن است اکسید تیتانیوم و اکسید زیرکونیوم مورد استفاده قرار بگیرد. با وجود اینکه اکسید زیرکونیوم باعث بیشتر شدن مقاومت در برابر شکستگی میشود، سختی و رسانایی گرمایی را کاهش میدهد. برای بهبود سفتی و مقاومت در برابر شوک گرمایی ممکن است مقادیر کمی کاربید سیلیکون به این ترکیب افزوده شود. نوک ابزار مقاومت بالایی در برابر فرسایش و دما دارند و ثبات شیمیایی بالاتر آن در مقاسیه با HSS و کاربیدها بدین معنا است که در حین برشکاری احتمال کمتری دارد که به فلز بچسبند و در نتیجه احتمال ایجاد زائده در لبهها کمتر است.
نیترید سیلیکون
در دههی 70 میلادی یک ماده برای ساخت ابزار بر اساس نیترید سیلیکون تولید شد. این مواد ممکن است حاوی اکسید آلومینیوم، اکسید ایتریوم و کاربید تیتانیوم نیز باشند. نیترید سیلیکون با آهن به خوبی ترکیب میشود و برای ماشینکاری فولاد مناسب نیست. نوع ویژهی آن سیالون است که حاوی سیلیکون، آلومینیوم، اکسیژن و نیتروژن است. این ماده در مقایسه با نیترید سیلیکون مقاومت بالاتری در برابر شوک گرمایی دارد و برای ماشینکاری چدن و ابر آلیاژها بر پایهی نیکل در سرعتهای متوسط برشکاری توصیه میشود.
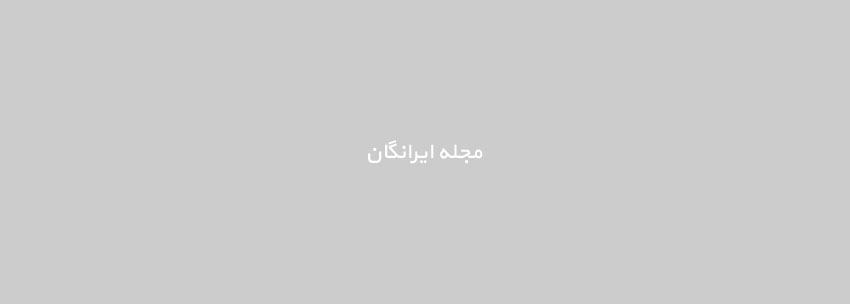
بورون نیترید مکعبی یا cBN
این ماده در دههی 60 میلادی به بازار آمد و پس از الماس دومین مادهای است که به وفور در دسترس است. ابزار cBN ممکن است به شکل سر ابزارهای کوچک یا به صورت لایهای از بورون نیترید پلیکریستالین با ضخامت 0.5 تا 1 میلیمتر باشد که تحت فشار بر روی یک زیر لایه همجوشی شده مورد استفاده قرار گیرد. در حالت لایهای، کاربید مقاومت در برابر شوک را بالا میبرد و لایهی cBN باعث افزایش مقاومت در برابر فرسایش و استحکام لبهی برش میشود. بورون نیترید مکعبی گزینهای استاندارد برای ماشینکاری آلیاژ فولاد با سختی 50 Rc و بالاتر است. سرعت معمول برش آن 30 تا 310 متر در دقیقه است.
الماس
الماس سختترین مادهی شناخته شده است. گرچه الماس تک بلوری بهعنوان ابزار مورد استفاده قرار گرفته است اما شکننده بوده و باید به صورت صحیح سوار شود تا ابزار بیشترین عمر ممکن را داشته باشد. الماسهای پلی کریستالین جای ابزار الماس تک بلوری را گرفتهاند. این ماده شامل کریستالهای مصنوعی کوچک است که در یک فرآیند پر فشار با دمای بالا با ضخامت بین 0.5 تا 1 میلیمتر با هم ترکیب شده و با زیر لایهی کاربید پیوند خورده است. نتیجهی کار به ابزار cBN شبیه است. جهتگیری تصادفی بلورهای الماس از ترک خوردگی جلوگیری کرده و مقاومت آن را بالا میبرد. الماس پلیکریستالین به دلیل خاصیت واکنشپذیری که دارد، برای ماشینکاری کربن استیل ساده یا نیکل و آلیاژهای بر پایهی کبالت و تیتانیوم مناسب نیست.
الماس پلیکریستالین برای برشکاریهای منقطع با هر سرعتی مناسب است و عمدتا برای ماشینکاری سریع آلومینیوم، آلیاژهای سیلیکون،کامپوزیتها و سایر مواد غیر فلزی مورد استفاده قرار میگیرد. سرعت برش آن معمولا بین 200 تا 2000 متر در دقیقه است.
سایر مواد
برای بهبود مقاومتابزار، پیشرفتهایی صورت گرفته است که از نمونههای آن نیترید سیلیکون تقویت شده با ذرات کاربید سیلیکون است.